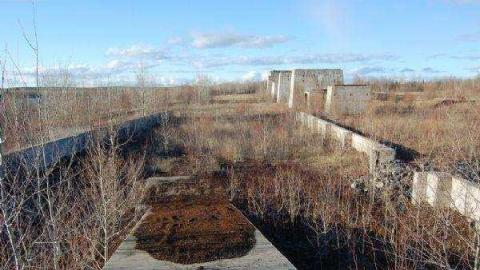
16 years ago
Griffith Mine
Ear Falls, Ontario
Recent status | Abandoned |
Location # | 15596 |
(Structures are no longer present at this site)
The Bruce Iron Range was first discovered in 1912, when the District of Kenora was being geologically survey.
It was during the early 1950's, when the Bruce Iron Range was being explored that comprised of 63 patent mining claims totalling 500 acres of land. Upon evaluating this area it was determined that the mining claims had uncovered a rich iron ore deposit. Further reports on the area had also stated that this discovery was located along the shore lines of Bruce Lake, that wasn't located to far from a small settlement known as Red Lake, Ontario, Canada. Explorations at the time were also considered to have been not done on this iron range by any previous company. Many iron ranges at this time were also being widely explored that resulted in building new iron projects in Ontario, Canada.
Within the year of 1953, the whole entire area was soon taken up for further exploratory work by a company known as the Iron Bay Mines, Limited. From 1953 to 1960, the claims which were staked had been thoroughly explored on the Bruce Lake Iron Formation. Most of this had also became establish when the company ended up drilling a series of 29 diamond drill holes, which totalled 13,062 feet in total length. It was within this time period when the Iron Bay Mines, Limited, would end up conducting pilot testing at Michigan College Of Mining and Technology, and also in Frankfurt, Germany. By 1960, the company would end up sending a few bulk samples to the University Of Toronto in order to determine the average head-grade of this iron hematite ore.
Further work was done on this property from 1963 to 1964, when another exploration company known as the Taconite Lake Iron Company, Limited, had took a 75 year lease on this property. The property at the time was additionally optioned from the Iron Bay Mines, Limited, who were the original claim owners of this discovery. During this time period the company would end up addressing the Steel Company of Canada, about its interest in this property. Eventually the company had purchased the optioning rights from Taconite Lake Iron Company, Limited. With this came a purchase by the Steel Company of Canada that had named this project the Griffin Iron Property.
Production from the Griffith Iron Mine was said to have been rather becoming achieved when the company had announce that the mine will be in production by 1968. In addition to this, the mine processing plant would end up having an annual output of 1,500,000 tons of ore when it was fully completed and place into operation. Once the processed pellets come from the mill, it will then be transported by a long 68 mile railway line that will connect this spur line with the Canadian National Railway Line. From here most the ore will than transported from a junction point to Amesdale, where the ore will than be shipped by cargo ships to the company's plant in Hamilton, Ontario, Canada. A deal was also made with the gas company to provide fuel to the future Pelletizing plant from the natural gas line that ran from the Trans Canada Pipe Line at Vermillion Bay.
Further construction was officially started in 1966. when the company was rather stripping away the overburden for future structure development. Most of this engineering phase would commence development stages on the company's Concentrator Building, Office building, a truck storage garage, and its vey own crushing facility. As development was under way the company would also bring in some of its own equipment. Some of this had included three electric shovels, one pay loader shovel, one rotary drill, two front end loaders, nine haulage trucks, a mobile crane, one diesel shovel, and five crawler tractors.
Company officials from the Steel Company of Canada Limited had also contracted out two exploration and development firms within 1966. These two historical company's became known as the Canadian Bechtel Limited, who employed 600 men, and the other company became identified as the Pickands Mather and Company, who employed 93 men. The Steel Company of Canada would also employ its own workforce of 55 men.
The North Pit was expected to be 1676.40 m long, 640.08 m wide and 335.28 m deep. Stripping operations began at the North Pit on June 1, 1966 and due to the location of the deposit which was partially under the lake, it was necessary to dyke off parts of Bruce Lake and also construct a tailings retention dyke between the north and south basins of the lake. By June, 1966, construction of a dredging disposal basin was in progress. The dykes, with an overall length of 3.2 km were completed over a two year period.
By 1967, the Steel Company of Canada Limited had started on further constructing this large scale mining operation. Most of this was done when new development was being achieved on the company's Water Intake Pump house, a road material crusher building, and its very own Plant Pump house. Further so the company's contractors had put full force in developing the Concentrator Building, Office Building, and Crushing Facility. As development escalated the company would also add more mining equipment towards this operation. Much of this had included one Rotary Drill, One Crawler Tractor, three haulage trucks, and one Diesel Shovel. Exploration procedures within the Griffith Iron Mine also continued when the Steel Company of Canada Limited. had conducted a series of 29 diamond drill holes that totalled 6,884 feet of core sample. Production from the open-pit had hoisted a total of 367,125 tons of ore within this year alone. However, most of the ore was said to have been stockpiled as the crushing and milling facility was not in operation yet. A full contract was soon warranted to the Pickands Mather and Company who became the controlling agents of this iron mining operation. In addition the contract company would end up creating a massive workforce of 182 men.
The year of 1968 was rather considered to be a very productive year for the optioning company and it's contractors. Within this year, the company's on-site milling and crushing facility was official in production by June. A massive Pelletizing Plant that had an annual output of 1,500,000 tons was officially completed, and in operation. During the start of production the milling operation was in a tune up phase which was only able to produce a daily rate of 2,300 tons of ore. Once the processed pellets had came from the plant, it would than be shipped by rail to a harbour that was located in Lakehead. From here the ore would than be shipped by a cargo fleet to the Stelco Plant in Hamilton, Ontario, Canada.
Much of the whole entire mining operation had mainly been confined to the North Ore Body Zone within this time period. Generally the whole entire operation is being conducted by the method of open-pitting. Even a series of Electric Rotary Drills are being operated in order to break down the ore from the open pit. As the ore become broken its than trucked by 45 ton truck. Development of the open-pit is mainly being done with an A.N.F.O Slurry Mixture that was being made on site by the Canadian Industries Limited.
Almost all construction phases had become conducted on the newly engineer dyke that would be 5,000 feet long. Further so, this whole entire project was being establish so that the ore body near Bruce Lake was cut off. In addition to this, the Steel Company of Canada Limited, had also installed water pumps with a capacity of 150,000,000 gallons per month. A series of explorations had also took place when nine diamond drill holes became driven within the hard rock, and would end up totalling 3,308 feet of core sample. During this time period the Steel Company of Canada Limited, would end up hoisting 1,120,977 tons of ore from the mine. Milling operation at the on-site concentrator was being put to full production when a huge amount of ore that totalled 2,450,139 tons was milled. Most of this became accomplished with a daily average of 7,487 tons of ore which was produced at the mill.
Production and development within 1969, was said to have been under full control of the Pickands Mather and Company. Company officials from the Pickands Mather and Company would rather put this operation in full force. Most of this became establish when a huge amount of ore was removed on a daily basis, and had its own estimation of 13,400 tons. Generally the company it self is able to process a total of 9,500 tons which produces 2,500 tons of iron pellets.
As development was rapidly expanding, the company would end up continuously pumping water out from the newly developed dyke. Another major construction phase was soon taking shape when the company decided to construct another 3,000 foot dyke. In nature this was done because the company had fear that the tailings from the mine would contaminate the waters of Bruce Lake during future dredging operations. Company officials from the Pickands Mather and Company would also make several modifications to the existing equipment within the concentrator. All of this construction phase was being done on the mine's Pellet Cooler which was estimated to go into production by 1970 Within 1969, the company would end up hoisting another massive amount of ore that totalled 4,046,688 tons. Even milling operations within the Griffith Iron Mine became outrageous when the mill had produce 3,883,233 tons, with a daily capacity of 10,638 tons.
The property during 1970, had additionally consisted of 63 patent mining claims, and an additional 4 licenses of occupation which included 500 acres, leased from Iron Bay Mines, Limited. Production that was taken from the open pit had amounted to 4,545,067 long tons of crushed ore of which 4,486,403 long tons were milled averaging about 12,292 long tons per day. Milling during this time period resulted in producing 1,632,581 net tons of Iron Ore pellets averaging 4,473 net tonnes per day. Much of the pellets from the mine were also shipped by railway line to the Lakehead and then transported by water to the Stelco plant in Hamilton, Ontario, Canada. Diamond drilling at this time amounted to 20 diamond drill holes, totalling 2,006 feet were drilled from the surface at the time. From all total production this had rather resulted in producing a total 3,339,116 tonnes of pig iron during the operating year of 1970. During this time the North American steelmakers, including Stelco had face sever problems of coal supply. In addition to this, unauthorized work stoppages had occurred within the coal industry which resulted in a halting coal production. Heavy purchases of metallurgical coal by Japanese and European interest had further restricted available supplies. With this came a sharp increase within the market pricing of Coking Coal that was required by several major steelmakers at the time. Other major plans at this time were aimed at changing marketing as the company had look for coal in western Canada and arrange trail shipments. At the time, technical problems had also occurred which impaired the ability of the mine to produce coal in specified quantity and quality. Stelco also had a researching center which was aimed at improving technology within the steelmaking industry. A total of 459 people were employed within the mine during this time period which Pickands Mather and Company were the managing agents.
During 1971, Crude Ore production with the Griffith Iron Mine had amounted to a total of 4,561,064 long tonnes from which 1,366,205 long tons of pellets containing 67.27% Fe and 2.97% SiO2, were produced. With this came a total of 6,535,022 long tonnes of material which was removed from the mine site. Stelco had also reduced it critical requirements for pellet SiO2 from 4.5% to 3.2% and meeting this new requirement that resulted in a slight loss of plant efficiency. The recovery of iron at this time was also improved by introducing fine screens in the mill circuit between the hydroseparators and the finishing magnetic separator. Further development within the mine had also included the erection of a new pumping station on the Trout Lake River, and the completion of the North Perimeter dike. This had also included the construction of the final 4,000-foot segment for a total length of about 15,000 feet, and further diamond drill exploration was conducted on the South Ore-Body in order to better define the ore-body and establish pit limits. Further so, a program of tailing re-claimation was instigated in corporation with the department of Lands and Forests, and, for aesthetic purposes, some 165 acres on the mine site were cleared.
In 1975, the Griffith Iron Mine had produced nearly 5,188,000 tons of Crude ore during this time period of operating. From all production it was reported that the Griffith Iron Mine would end up producing 1,499,000 tonnes of pellets from the company's operation. Further statements had reported that the mine contain significant amount of ore in order to maintain output at the mine until 2005.
Production during 1976, had amounted to 5,453,583 tonnes of crude ore that produce 1,546,514 tons of pellets grading in excess of 68.78% Iron and 77,480 tons of sponge iron containing 90.40% and 82.40% metallic iron. The total material which was produce from the company's pit from years of operation was 13,029,536 long tons. A completion of the second phase of diking and dewatering of the North Pit, which permitted the movement from the south end of that pit in 1976. Within this time period, the SL/RN Kiln had operated to the end of July, at which time the plant was shut down for the balance of the year due to a substantial decrease in the price of scrap at the steel mill.
The Griffith Iron Mine was operated by a wholly subsidiary of the Steel Company of Canada, Limited, that was manage by Pickands Mather and Company. Milling which had taken place within the Griffith iron Mine property had process 5,602,533 tons of ore that had gave a production of 1,538,534 tons of pellets containing 66.71% Fe (dry) and 3.60% Silica. From all production it was reported that the total ore, waste, and overburden removed from the open pit had resulted in mining 13,850,261 long tons. The SL/RN Direct Reduction Kiln had not been operated in 1878, due to low prices of scrap steel. Other development that achieved during 1978, resulted in the completion of a diversion of waste material flow from the west side of the plant complex, and seeding for reclamation of the unused secondary tailings disposal area, within 1978. Some more equipment was also installed for the recovery of fine iron from flotation tailings and installations were commenced for flotation automatic control, to be completed in early 1979. No additional exploration diamond drilling had also been carried out on this property during the operating year of 1978.
Production during the year resulted in milling an estimation of 5,304,300 tonnes of crude ore that was produce from the pit in 1979. From all production it was reported that the mine had produced 1,500,000 tons of natural pellets containing 66.72% dry iron and 3.56% Silica. The total amount of waste, ore, and overburden from the pit was estimated to have mined 12,576,400 long tons. Further diamond drilling was also done on the property which resulted i1,849 feet of diamond drilling for the purpose of bank satiability studies. It was also during the summer of 1979, when 639,713 cubic yards of lake bottom material was dredged to allow further development of the South Pit. The movement of the ore in the South Pit would additionally commence during the operating year of 1980. During 1979, capital expenditure was made towards recovering fine ore from the flotation tailing and the flotation tailings.
The property of the Griffith Iron Project was additionally added to the company's assets in 2010. Work was also done during this time period which resulted in completing 1 diamond drill hole on the southeastern shore of the North Pit. DDH-GF-01, was 429.16 m in total length and had intersected magnetite mineralization at various grades from 219.80m to 29.16m depth. Assay results from this exploratory work had returned 4.95% to 38.78% Fe, including 2 meters of mineralization grading 38.78% Fe from 419.54m to